All posts by Max Vollmer
Cottonwood Bowl
Cottonwood is a very soft wood and for that reason it is not traditionally thought of as material for turning bowls. However, this morning I drove past a couple of guys who had just cut down a dead cottonwood tree in a front yard and I asked for and was given one of the rounds to cut up and try to turn. Although dead, the tree had been standing out in the weather and was relatively wet, making it difficult to cut cleanly with turning tools. Sanding was slow as well. But a pleasing shape can still be realized with a little patience. This bowl is 5″ deep and a little over 6″ across.
Planning for Cherry Dresser
Today, I am starting in earnest on the design for my 6′ tall cherry dresser with 4 graduated drawers below and 2 raised panel doors at the top which will open up to 4 pull-out bin-drawers. To be made with knot-free, wide plank, black cherry lumber from Pocahontas County, West Virginia, that I’ve been air drying for over 30 years. (Click on any image to enlarge)
Big Leaf Maple Burl Bowl
Pots & Bowls
Weed Pots in February
This is what you can do with a weed pot/Ikebana vase in February. I clipped one branch each from my ornamental crab, ornamental plum, and Mountain ash trees in the back yard. The pot was turned from a “defect” in an otherwise clear Oregon black walnut board. (Click on the image to enlarge)
The walnut pot/vase by itself is 5″ tall, 1.75″ in diameter, and has a 5/8″ diameter slug of steel bar hidden in the base for stability.
Ikebana Vases
I have a hard time calling these weed pots, although that is their genesis. The one on the left is Wenge and the one on the right is in Adaman Paduak. They are drilled out and weighted with 5/8″ steel plugs on the bottom for stability.
I started turning utilitarian items (rolling pins, bowls, chair legs, etc.), but I’m starting to see the potential for sculpture. (Click on the image to enlarge)
Two White Oak Bowls
These two bowls were turned from two blocks of wood that were originally side by side in the same oak board, yet they differ substantially in appearance. The bowl on the right came from the center of the board, closer to the heart of the tree, and the one on the left was a little further from the center. The wood grain effects are noticeably different, and the coloring of the wood is slightly different. The curve of the sides varies slightly from one to the other, and the diameter of the bowl on the right is about one inch greater. Offered for sale together, a discerning buyer would have a clear choice to make. There’s no question which one I would pick. (Click on the image to enlarge)
New White Oak Bowl
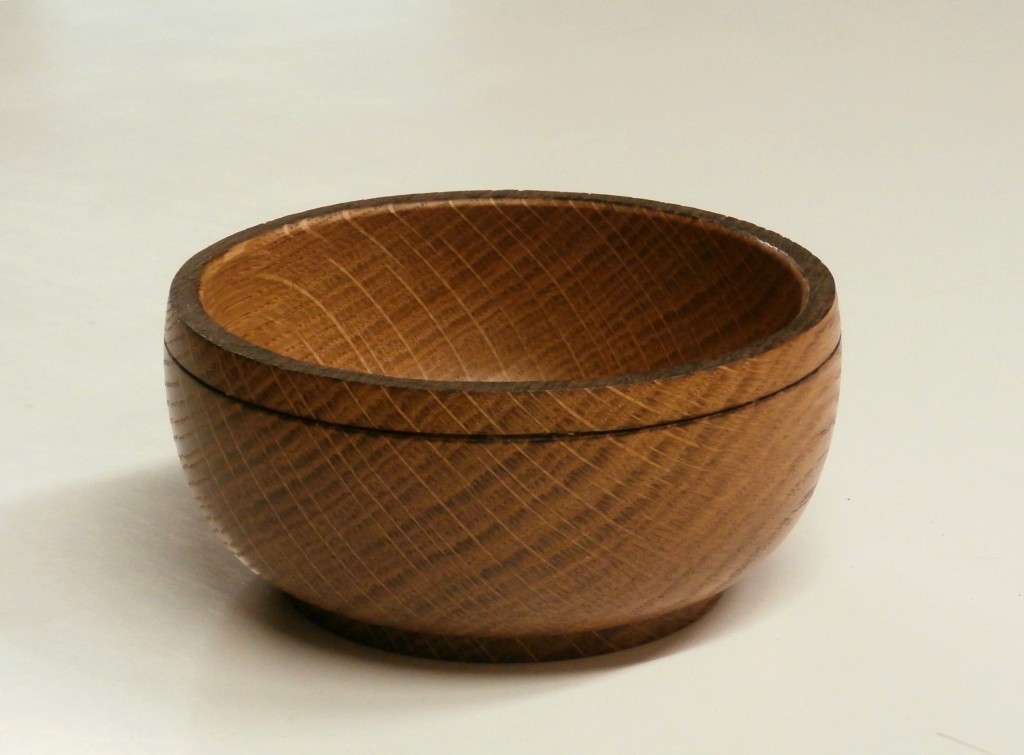
I’m partial to this basic “containing” bowl shape and here it is in white oak. The oak has a nice warm brown tone when finished with just beeswax. I used another piece of oak to burnish the edge while the bowl was spinning on the lathe. (Click on any image to enlarge)
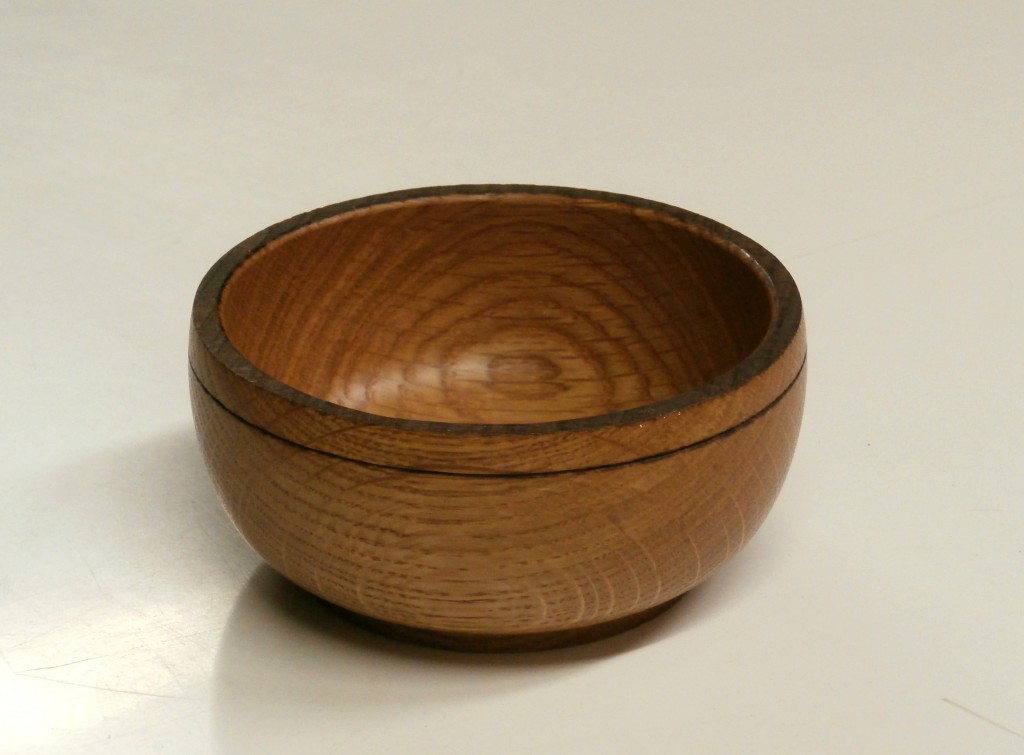
Rocking Chair Repair
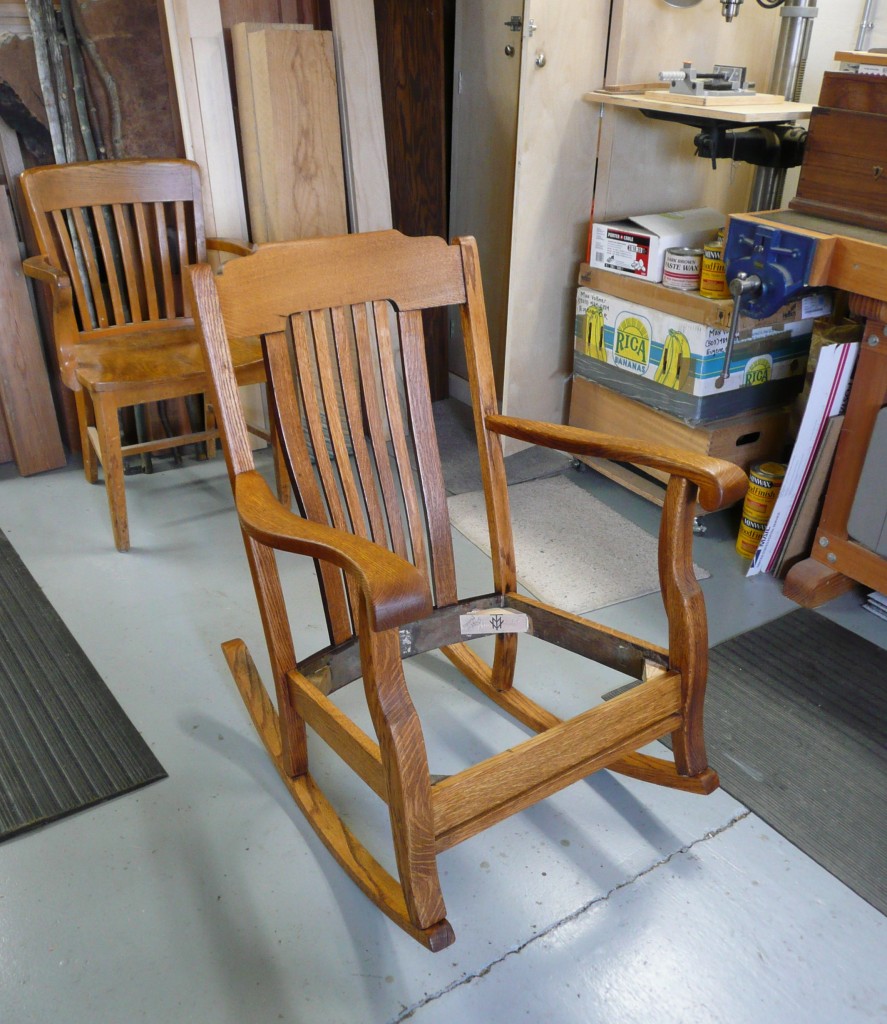
I get more rocking chairs in for repair than any other piece of furniture. No surprise, really. They are favorites in most households and the very fact they are rocked back and forth thousands of time puts a strain, over time, on frames. This nicely proportioned solid oak rocker from the early 20th century was typical in that the original hide glue that held the joints together was nearing 100 years old and turning to powder, loosening all the parts. (Click on any image to enlarge)
My first step was to disassemble the chair as much as possible.
Then any missing or broken pieces are fabricated anew. Old finish is removed via stripping and/or sanding if the client requests it be done, as happened here . Then the chair is reassembled, in this case with new dowels and reconditioned seats for the dowels.
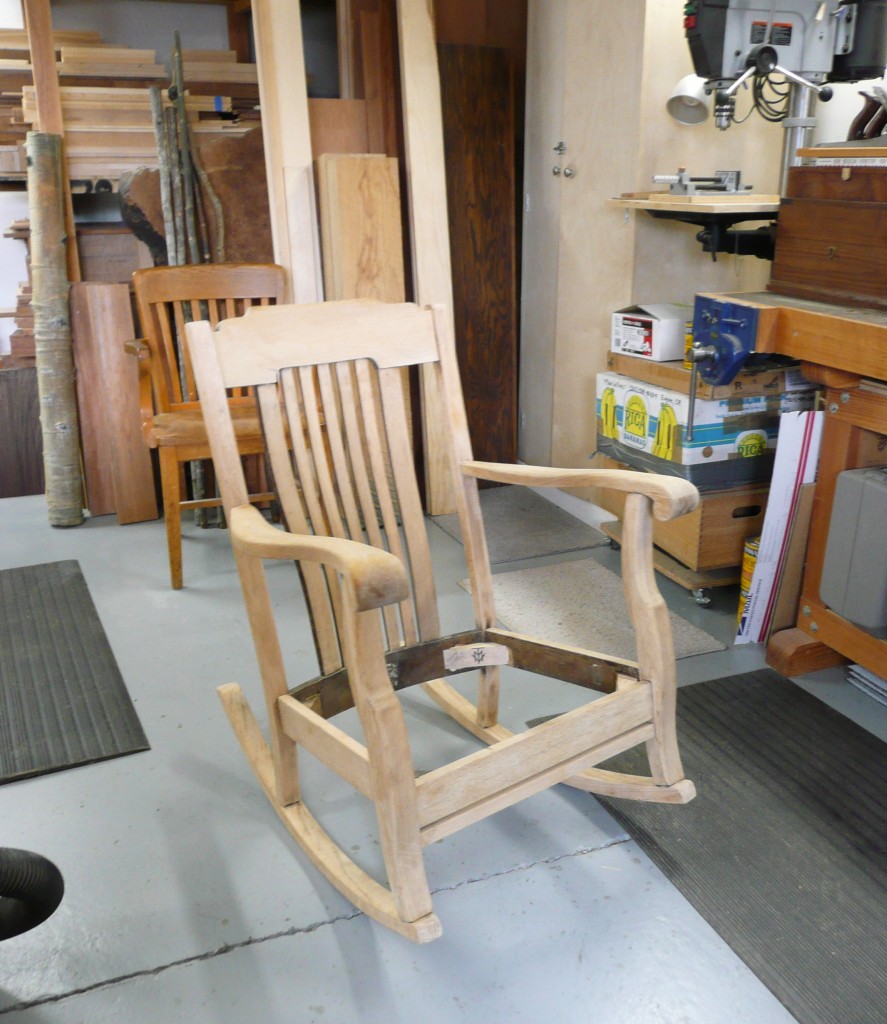